Subchapter 3.9
Robot safety
We have summarized the most vital information about safety concepts for your robot application below. Learn how to prevent access to hazards, limit robot motion, and ensure safe human-robot interaction. Discover the significance of safety fencing, advanced detection systems, and the importance of planning collaboration workspaces.
Standards and essential rules for robot safety
Robots are incredibly versatile, offering economical automation solutions. However, they can also be quite dangerous
Large, hiqh-speed robots, may cause very serious injury by crushing and impact. Therefore, robot safety has been standardised internationally in (EN) ISO 10218-1 and -2 and for the USA in the almost identical ANSI/RIA R15.06. Additionally, a standard for mobile robots has been published with ANSI/RIA R15.08. Some vital safety rules are presented below.
Robot safety is build on three elements:
- Prevent access by people
- Limit robot motion
- Make physical contact safe
The third element, making physical contact safe, is a relatively new concept, often referred to as collaborative robot operation. It means a specially designed robot system and an operator work within the same workspace or overlapping workspaces. First, the collaboration workspace and the desired human and robot interaction must be planned. Then, the risks are identified, and appropriate safety measures are implemented.
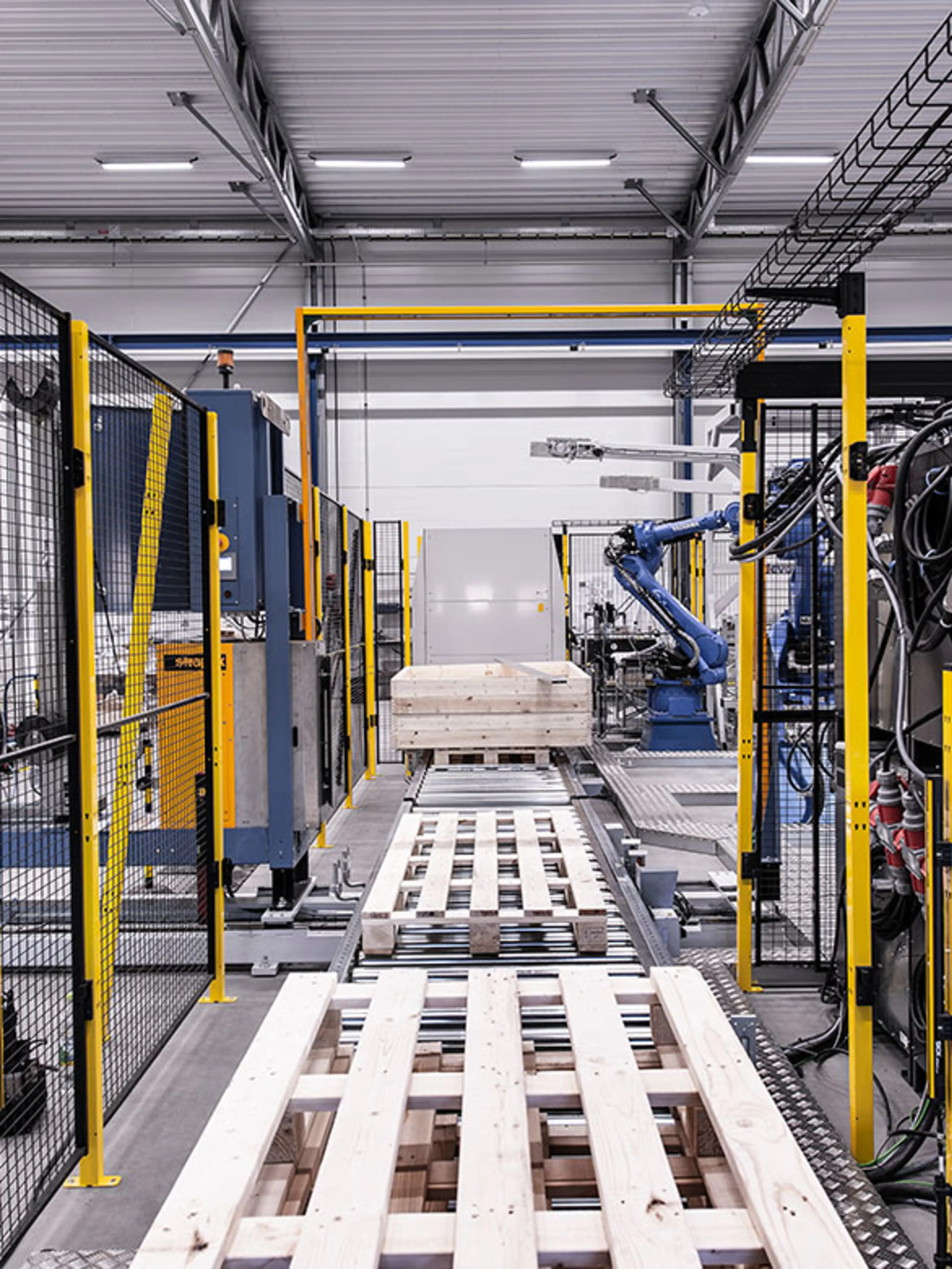
What is a “collaborative robot”?
The most advanced safety measure is the use of a collaborative robot, sometimes referred to as a “cobot”.
A collaborative robot operates at limited force and speed. Humans encountering a moving collaborative robot will not be injured, although they may feel some pain. Years of extensive testing have resulted in a list of force, speed, and energy limits that humans can endure when subjected to physical contact with machine elements (see ISO TS 15066).
Collaborative robots moving within these limits may be considered safe for human-robot interaction. However, that does not mean such applications are automatically safe. The entire context of the robot and the tool handled by the robot (the end effector) must be considered carefully.
Example:
- Imagine sitting next to a robot handling a syringe with poisonous liquid. The speed and force of its movements suddenly become secondary concerns.
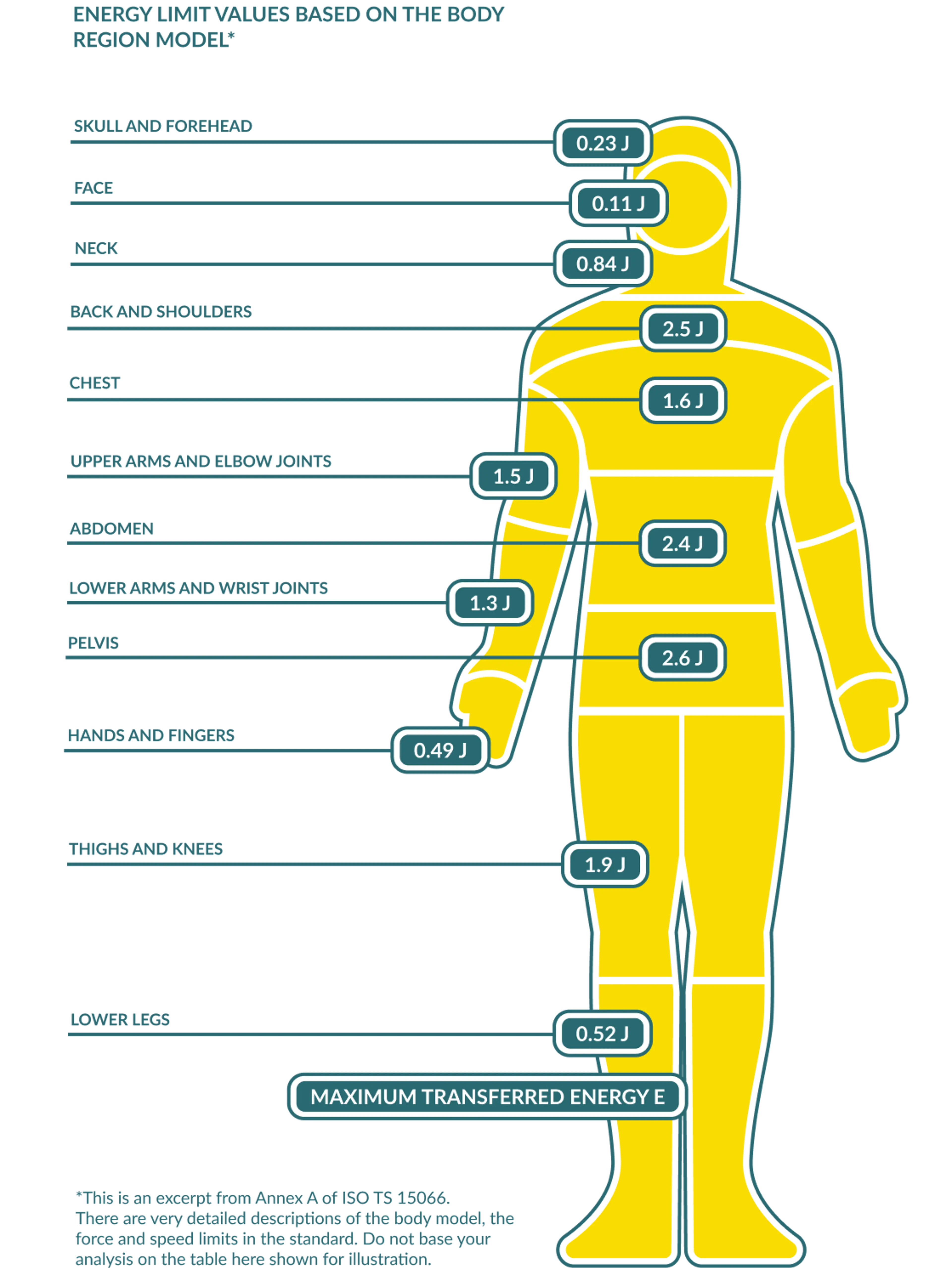
Safety in collaborative workspaces
In the graphics, a human operator and a robot share the collaborative workspace.
Safety measures:
- A hazardous robot must not move in the collaborative area if a person is present.
- Depending on the distance and motion speed of the person, the robot may have to slow down and stop as the person approaches.
Safety Fencing:
- Safety fencing is still necessary in some collaborative applications today and will continue to be so in the future.
- Fences take on new roles, such as demarcating a collaboration area from ordinary workspaces and walkways.
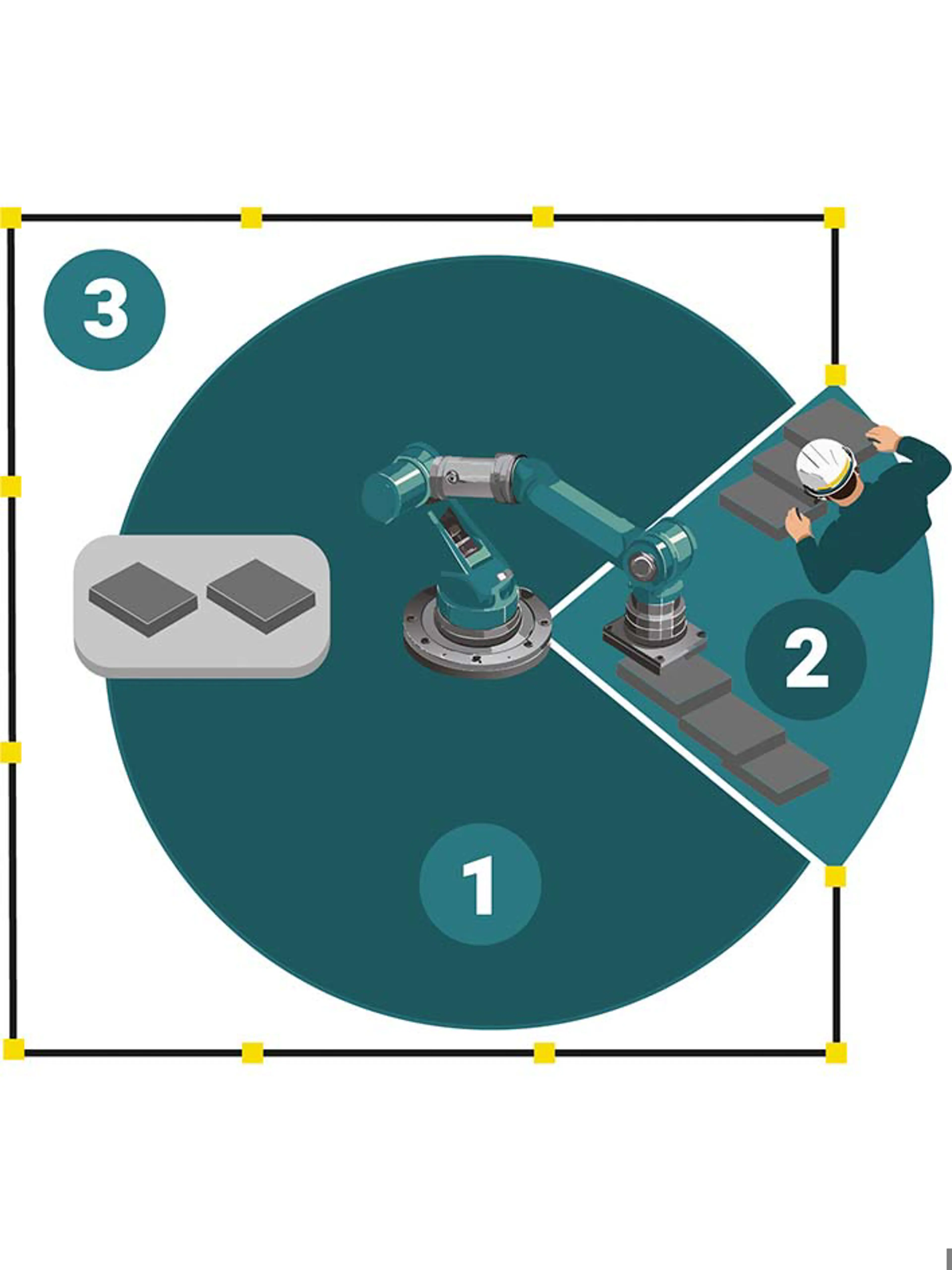
Industrial robot safety
Robot safety largely depends on closed "cells" with fencing and access doors. But in many applications monitoring systems are additionally needed or may even replace the robot "cage".
Advanced detection systems:
- In many robot cells, a combination of safety fences with doors, light barriers, and range scanners is used.
- The most advanced form of detection system is a 3D-camera. It needs to be installed at a sufficient height above the workspace to ensure it “sees” all the areas in which persons may move.
Beware of persons remaining inside the hazard zone behind the detection devices. If that is possible, additional safety measures may be needed.
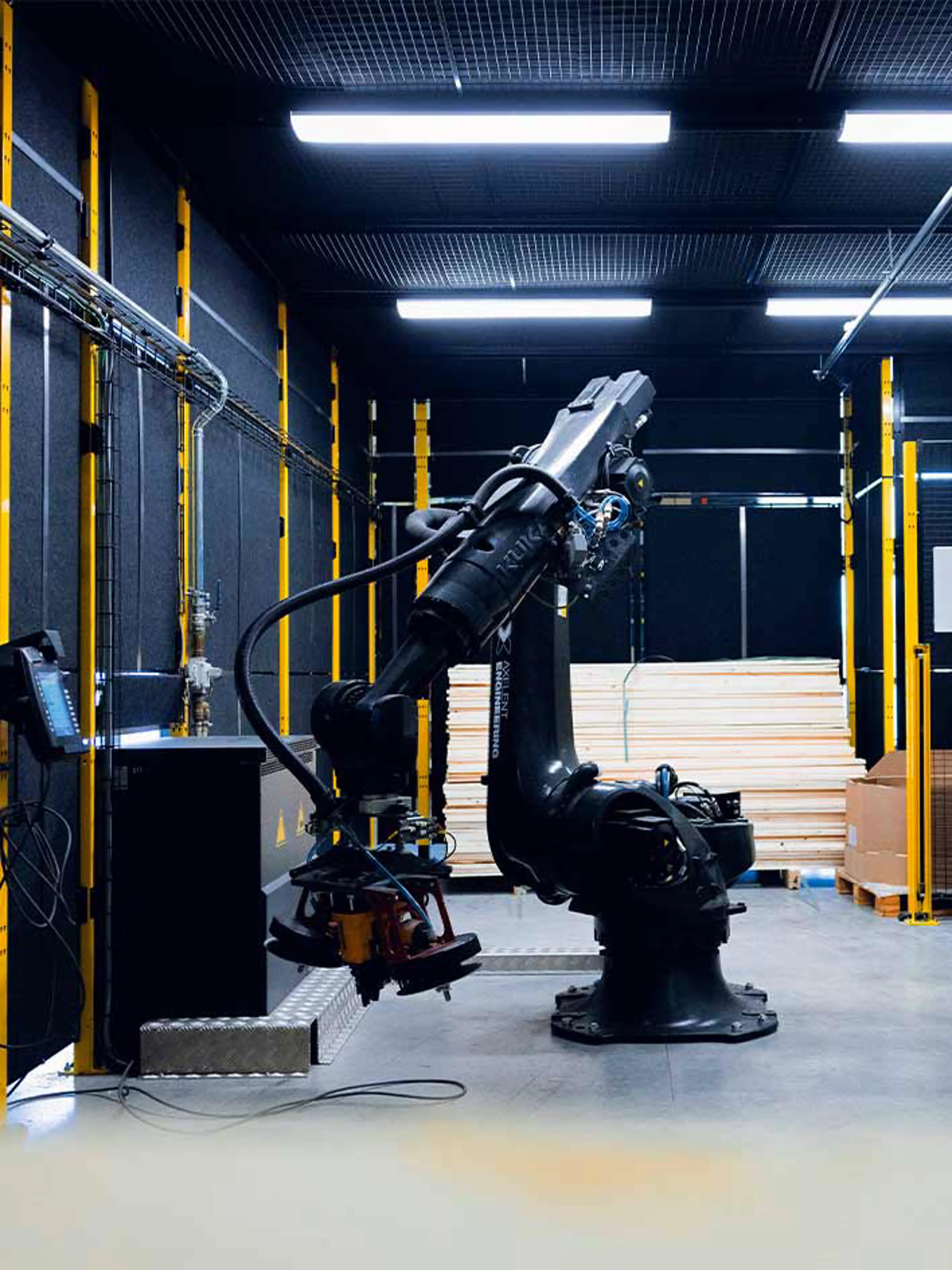
Safe zones for robots
Fencing may be used to create a “protected space”, but it must not normally be used to define the “limited space”.
Robots colliding with fences at high speed or with significant force can cause deformation, even in robust fencing, posing potential safety hazards. Additionally, fences may allow individuals to stick their fingers through the openings, increasing the risk of injury. To mitigate these issues, a minimum clearance of 120 to 200 mm must be maintained between the limited space and the outer edge of the fence. Read more about calculating and determining the proper height and distance of guard fencing in chapter 3.2 “Selecting machine guards”.
Therefore, relying solely on so-called “robot-safe” fencing is insufficient. Instead, implement appropriate limiting devices to ensure safety, such as:
- Safety-rated motion control software (conforming to at least PL = d according to (EN) ISO 13849-1 or SIL 2 according to (EN) IEC 62061)
- Space-limiting mechanisms or physical hard stops (e.g., stopper blocks and pins)
- External limiting devices (e.g., mechanical stops or proximity switches)
Fence is meant to keep people out, not the robot in.
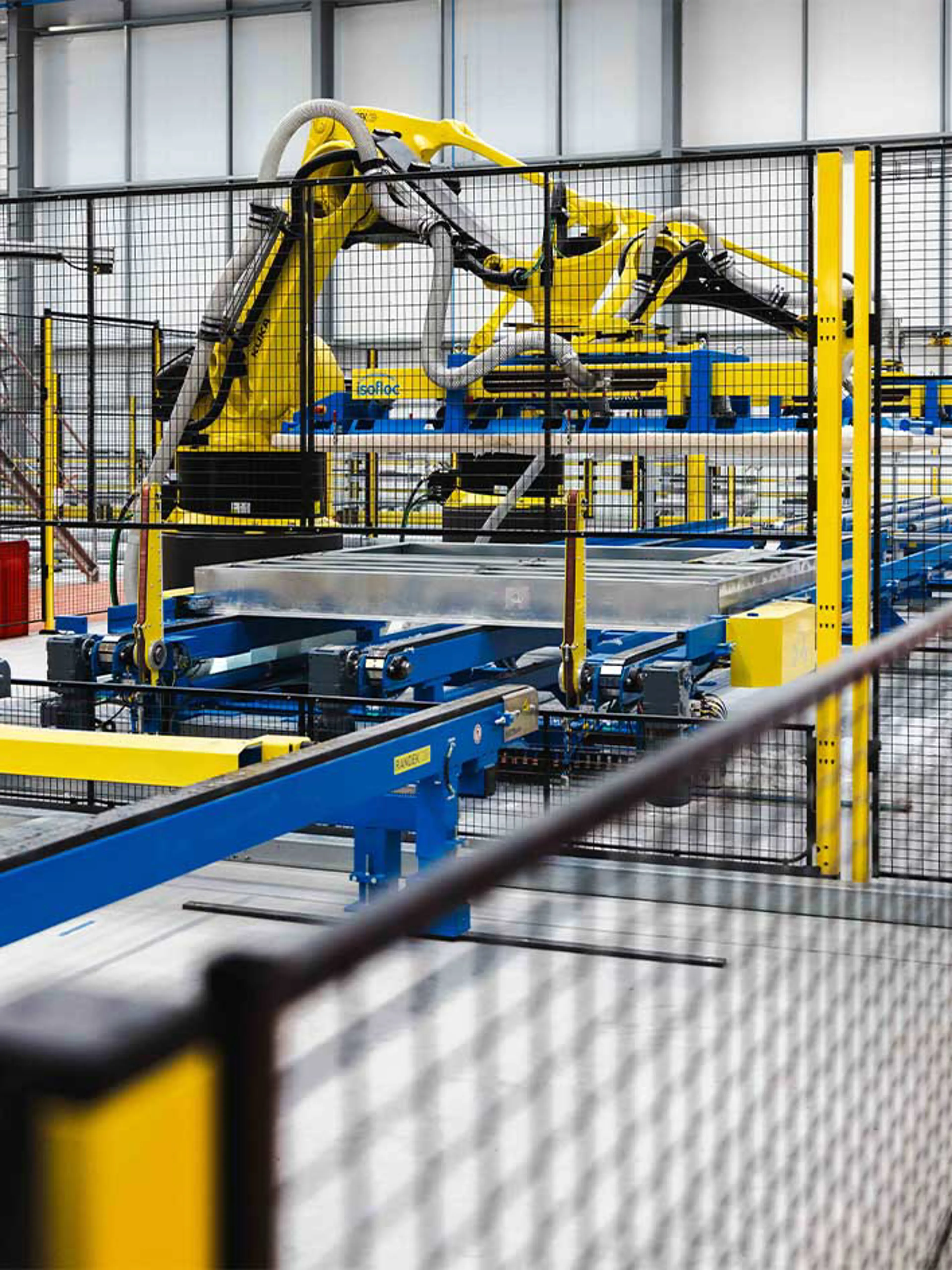
“Robot-safe” fences – concept or misconception?
Many people ask for “robot-safe” fencing or point to test results of fence manufacturers showing impact resistance of 2000 joules or more.
The question itself reveals a misconception about robot safety. Robot safety standards require that robot motion be limited by means other than fencing or other safeguards.
A robot‘s motion range depends on its size. Often this “maximum space” is much bigger than needed for the operation at hand. Since system designers want to use as little floor space as possible, the robot is programmed to keep to a much smaller “limited space”. Then fences, light courtains and range scanners are used to define a “protected space” around the limited space that persons must not enter.
However, a safety distance is practically always needed between the limited space and the protected space. Why? Because the robot needs time to slow down and come to a standstill when a person entering the protected space is detected (by a light-barrier, scanner, camera, or door switch).
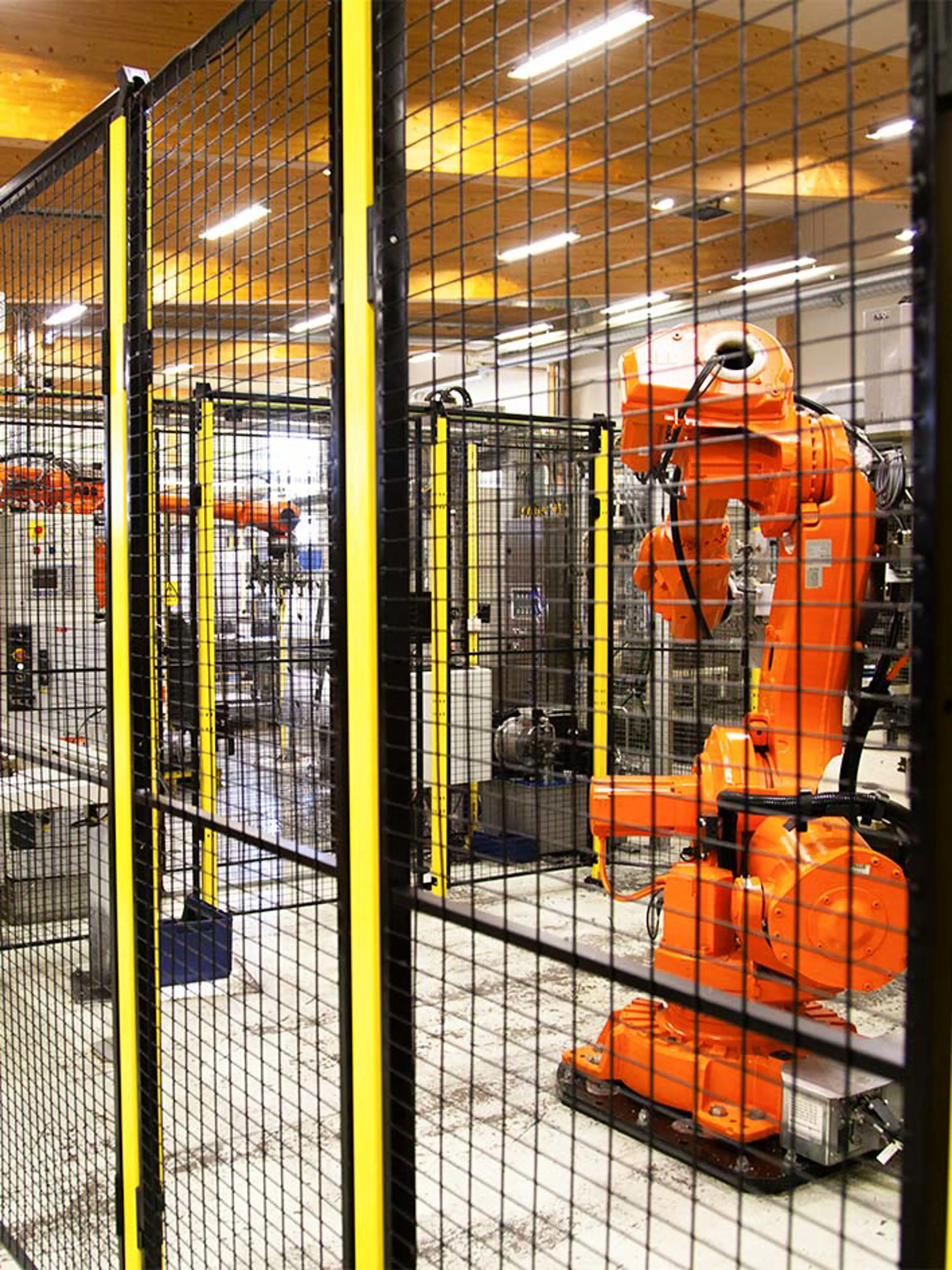
This infographic illustrates how to think critically about safety distances for industrial robots. Learn why guard fencing matters, how accidents occur, and when fences might not be the only solution. Discover the key considerations to keep people safe around robots.